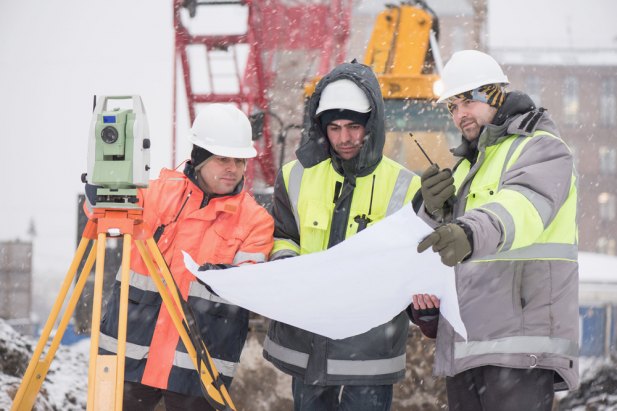
Six ways winter weather may affect your commercial construction project
Welcome to another winter in the Midwest, the season of bitter cold, freezing rain and blowing snow. A season for hunkering and hibernating, winter can also be a season where the construction phase of your commercial project can slow dramatically or halt altogether.
If you find yourself in the midst of construction on a project that isn’t winter-ready, you can expect to face a few hurdles toward completing your project. How much it affects you will depend both on how agile and how prepared your commercial construction company is to face the capricious nature of our coldest season.
Construction during winter can bring additional obstacles.
Frozen subgrade material can lead to settlement. If completing site grading and site subgrade preparation activities in cold weather, specific attention needs to be paid to frozen material. Moisture can become trapped in frozen material, making it all but impossible to achieve proper compaction, and when the ground thaws in the spring, the moisture is released and settlement can occur.
Concrete can be compromised. If exposed to freezing during the first 24 hours of being poured or placed, concrete can lose up to 50 percent of its strength, according to the American Concrete Institute. Sometimes, in more moderate temperatures, sheeting or concrete blankets can solve the problem. In colder temperatures you’ll need to bring in provisions for heat and cover to protect newly poured concrete.
Mortar and grout require heat. The Brick Institute of America warns that cold weather inhibits the absorption of moisture and thereby reduces compressive strength, bond strength and water penetration resistance. In some cases, heated bricks can do the trick; otherwise, you’ll need provisions for heat and cover to protect newly placed brick and block.
Drywall can be slow to dry. Mud drying time depends greatly on temperature and humidity, and in winter weather those factors could delay painting and applying other wall finishes for days. The solution, of course, is heat and humidity control.
Paint can freeze. The same goes for painting. In 35-degree weather or below, you can expect big challenges with paint. Cold temperatures lead to slower drying time, inconsistent color and water spots. The paint also won’t last as long, and it will be more susceptible to mildew and other issues. That means you may want to delay painting at times and/or bring in special cover and heating systems.
Schedules and budgets may need adjustments. With all the complications detailed above, you should plan ahead and be prepared for schedule changes and budget modifications. In addition to potentially extended durations for work activities and additional costs for everything from fuel for onsite heaters to concrete blankets, you should be aware of the risks of building in in the winter season.
One solution is one team.
Ideally, contractors will have the exterior finished and weather-tight before the polar vortex hits, allowing them more control over the schedule promised to the building owner. But it isn’t always possible.
That’s where a design-build team offers you better insulation (sorry, couldn’t help ourselves) from such budget and schedule changes, not just during winter but throughout the rest of the year too. Because the designers and builders all work together on the same team, they have improved ability to phase design and construction activities to keep your project moving forward even in the midst of winter. And in the upper Midwest, where winter seems to last eight months of the year, that kind of resilience saves you time, money and trouble.
You may also like “When it comes to commercial construction, to everything there is a season.”